Custom Furniture Just the Way You Imagined
What can we build for you?
About us
Smell the Fresh-Cut Lumber
Everyone who wanders into Roger’s shop automatically stops at the door and takes a deep breath. It’s amazing how many memories are stirred up by the smell of a wood shop. Whether it reminds them of their granddad’s shop or a walk in the woods, everyone has a story to share just from walking in.
But then they look around at the beauty of the fresh-cut lumber and feel the smoothness of the latest project on the bench and they know that new memories are built here every day.
Bayne Custom Woodworking based in Mt. Juliet, Tennessee designs and builds custom furniture in the Middle Tennessee area. From the beginning of a project design in 3D design software to selecting the wood at one of our local mills to completion in the workshop, the owner Roger Bayne makes every measure and cut.
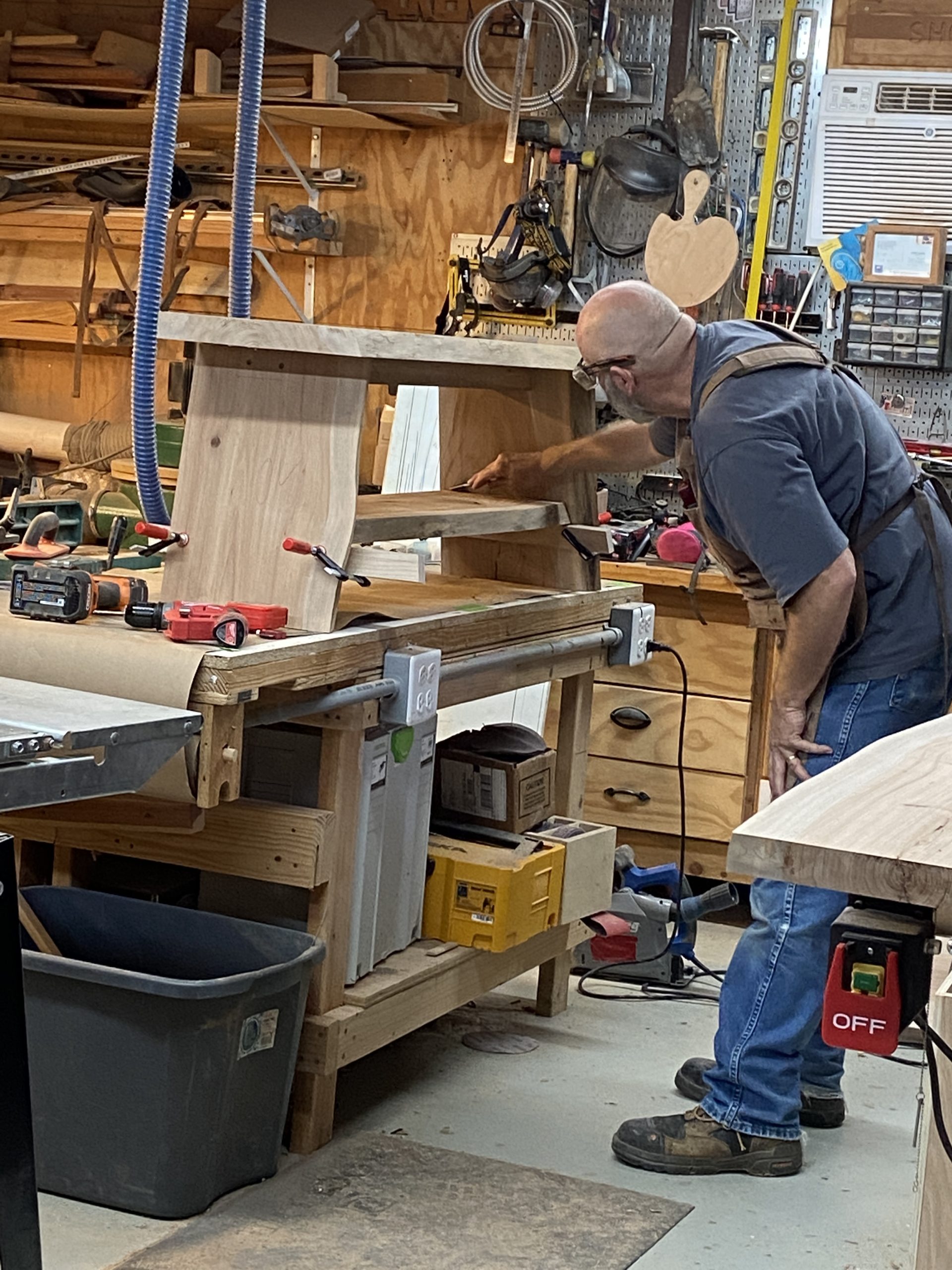
working with us
why choose us
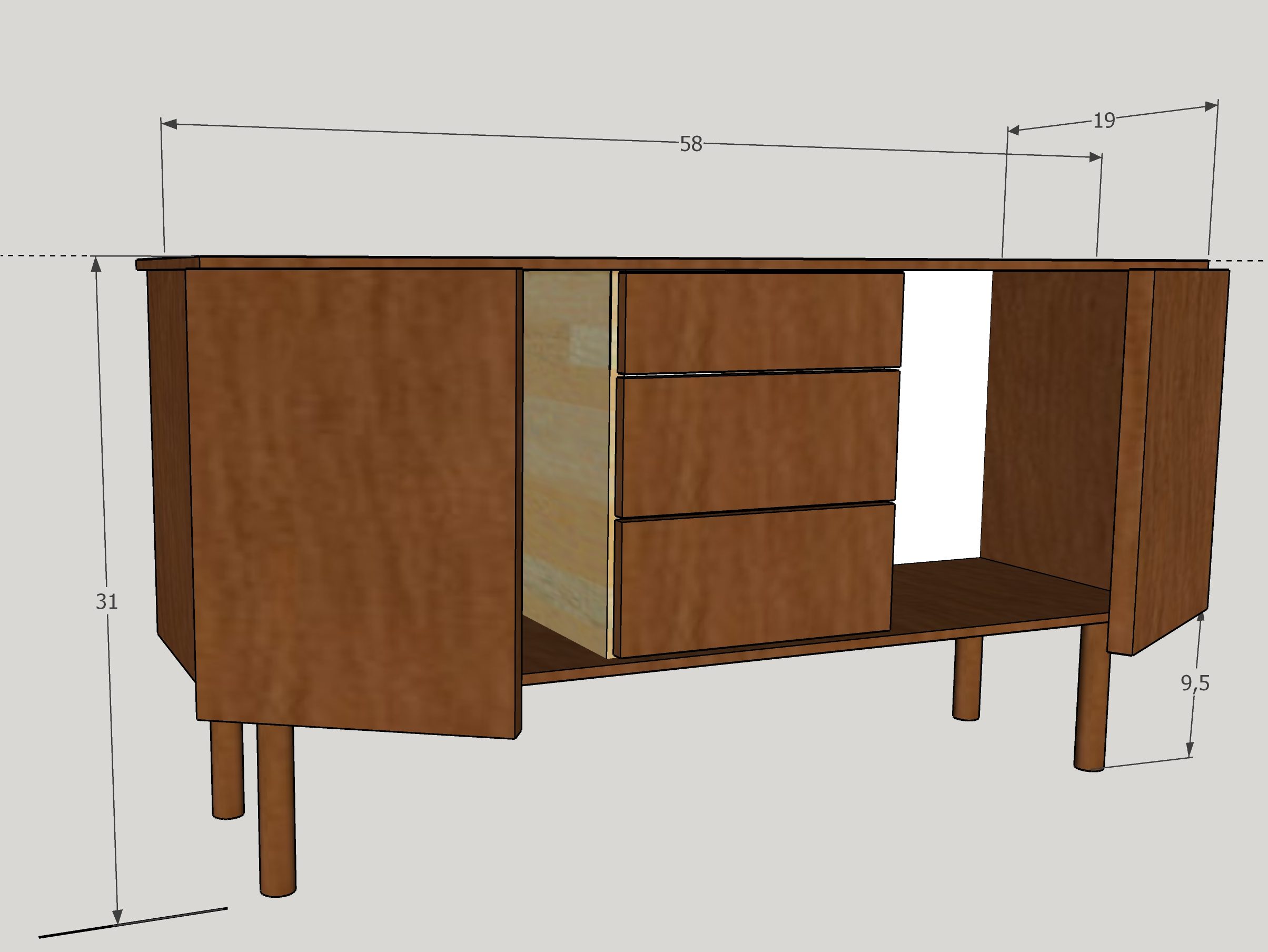
Every project starts with a detailed drawing
We want to make sure your piece of furniture is exactly the way you want it. We take your dimensions and draw up the exact piece for you in Sketchup – which allows our customers to know exactly what the final results will be.
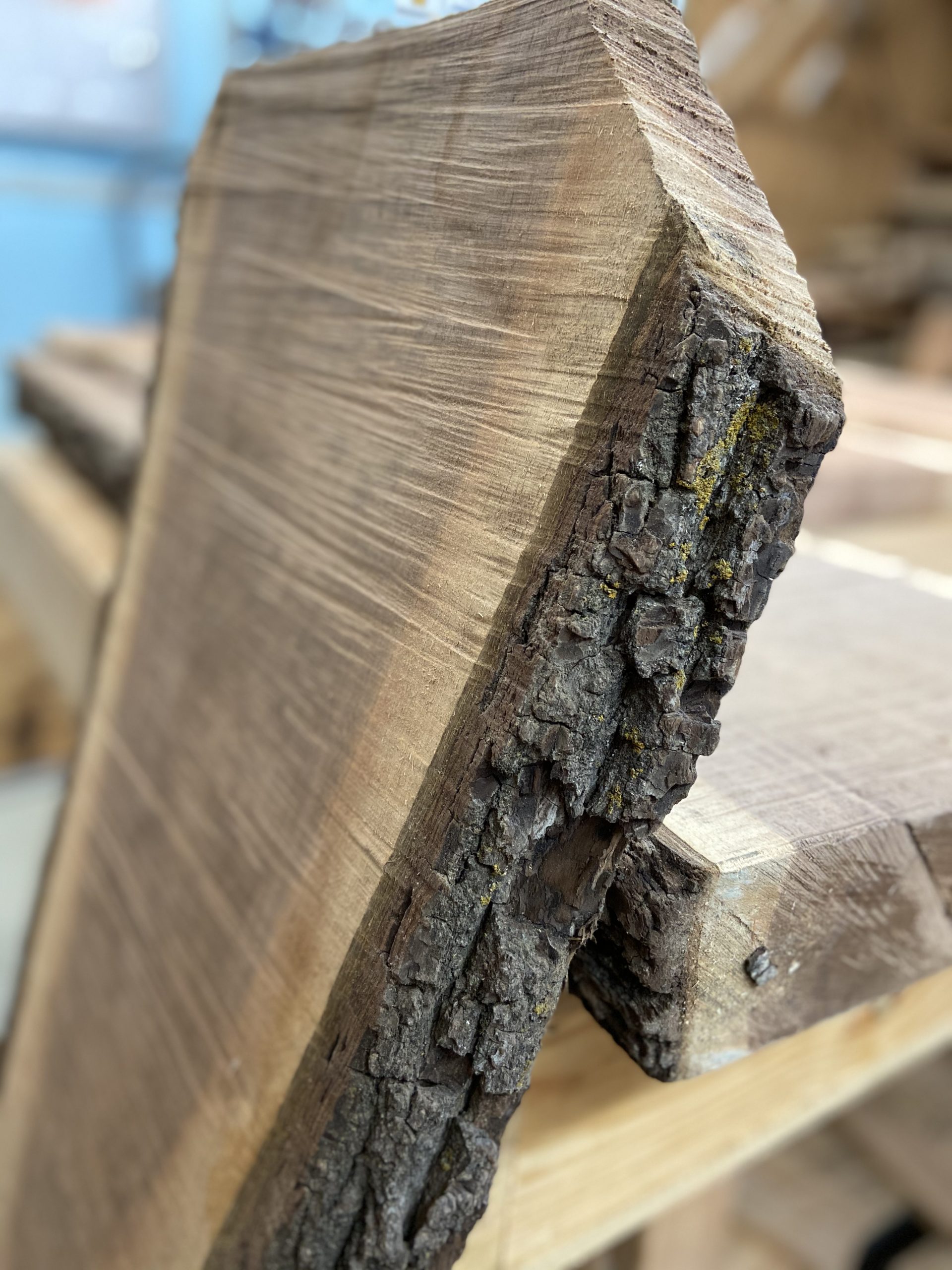
We use real wood from lumber mills
We source our wood from local lumber mills in Tennessee and occasionally harvest lumber from Indiana. The raw material is processed in our shop in preparation for each project.
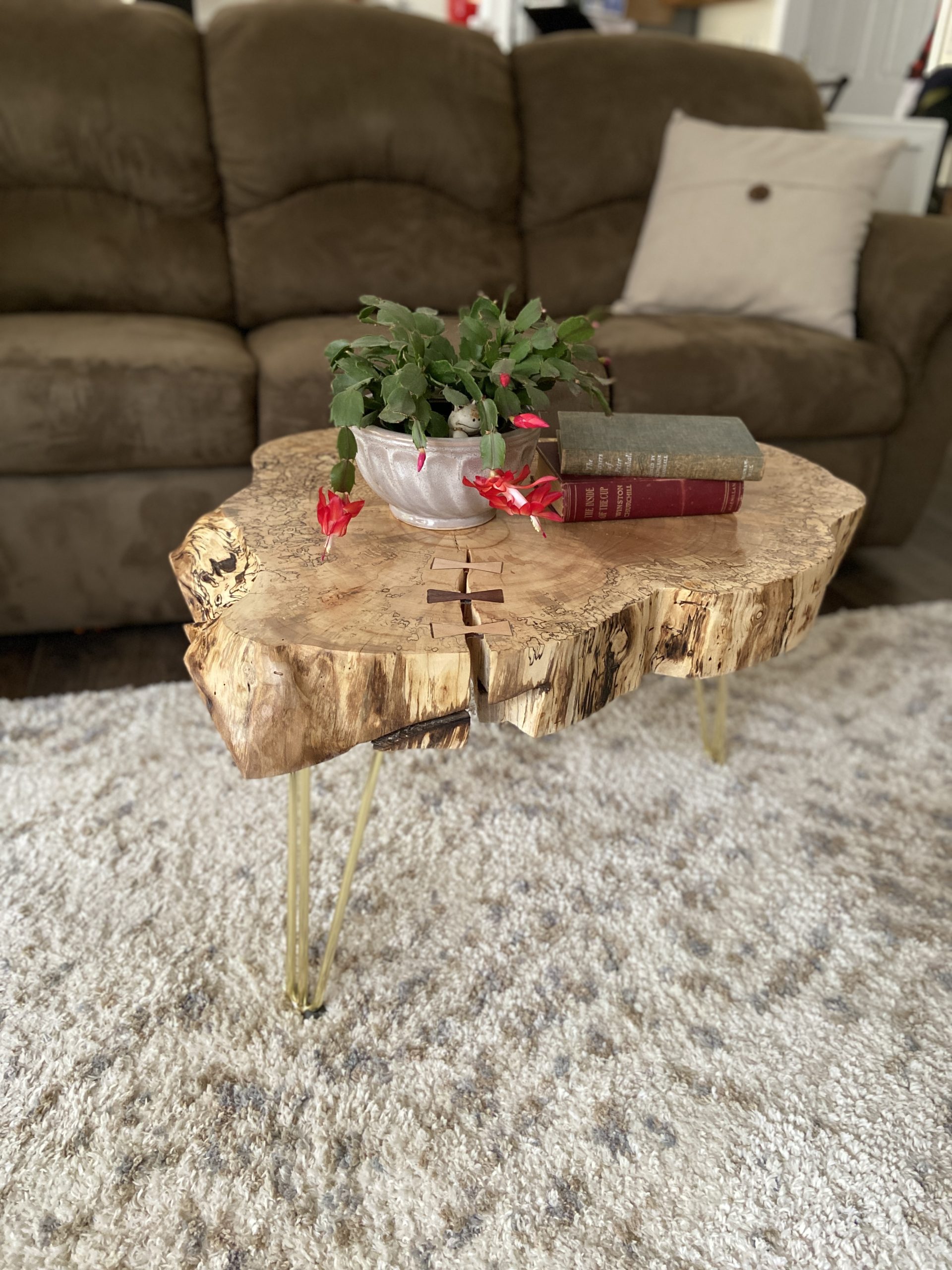
Unique Creative Designs
The beauty of sourcing wood ourselves allows us to find treasures that don’t fit the “normal” mold. We are always asking the question “What could we make with this special piece of wood.“That’s where our creativity shines!
what we do
Our Services
We build custom furniture in our small shop in the Nashville, Tennessee area. The hardwood we use is sourced from local lumber mills and then planed for each project in our shop.
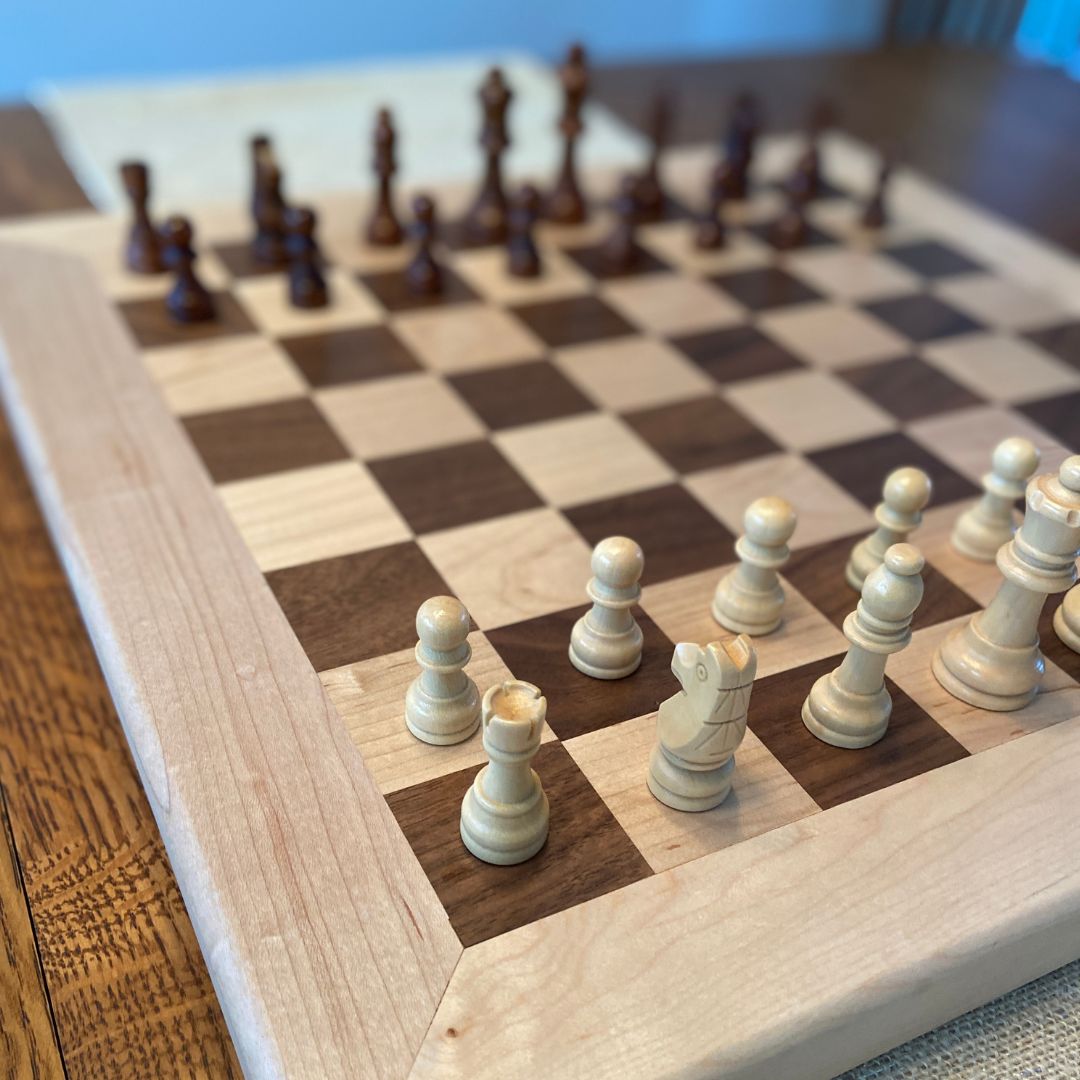
High-Quality Pieces
Chess and Checkerboards, children’s blocks made of cedar, cutting boards, and recipe stands all made from real wood and finished to stand up to the test of grandkids and messes. Check out our products to see what we have in stock or just ask, we’re happy to fulfill orders as soon as possible.
working with us
our gallery
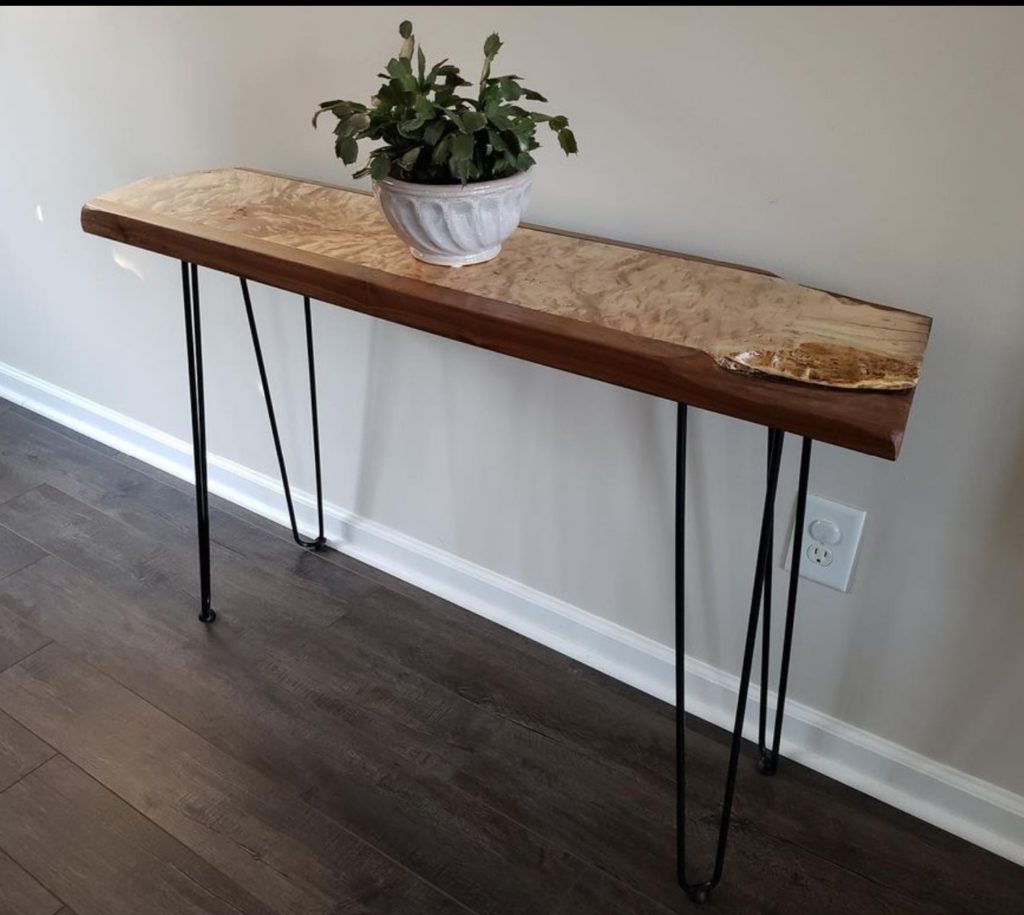
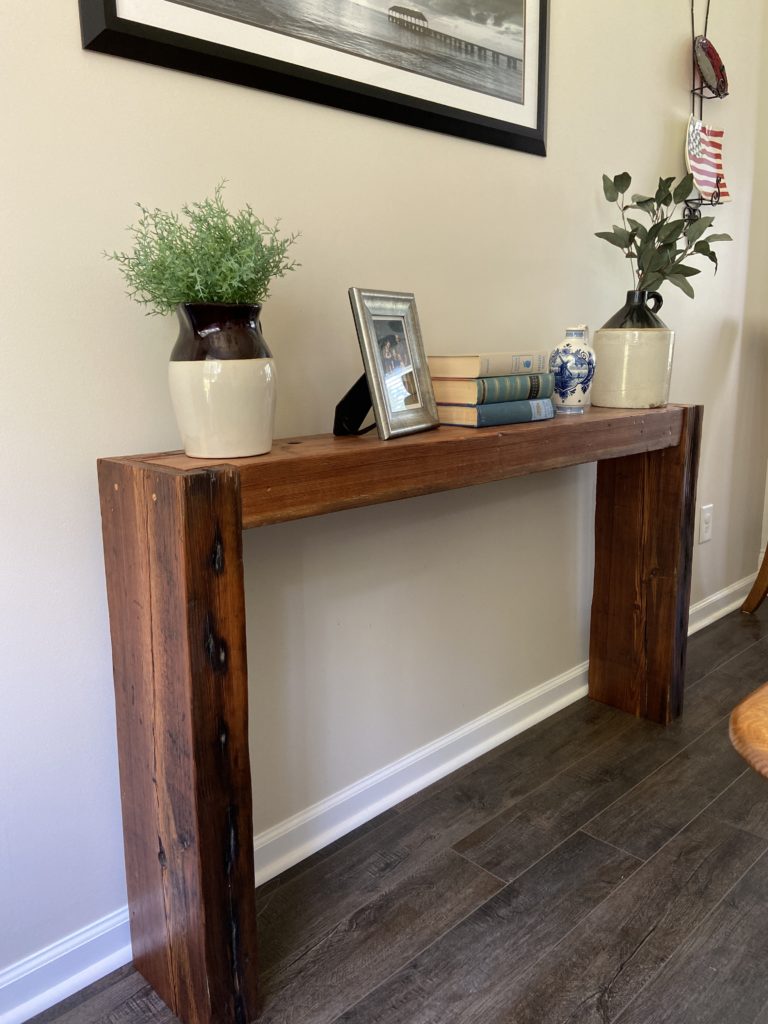
Beam Console Table
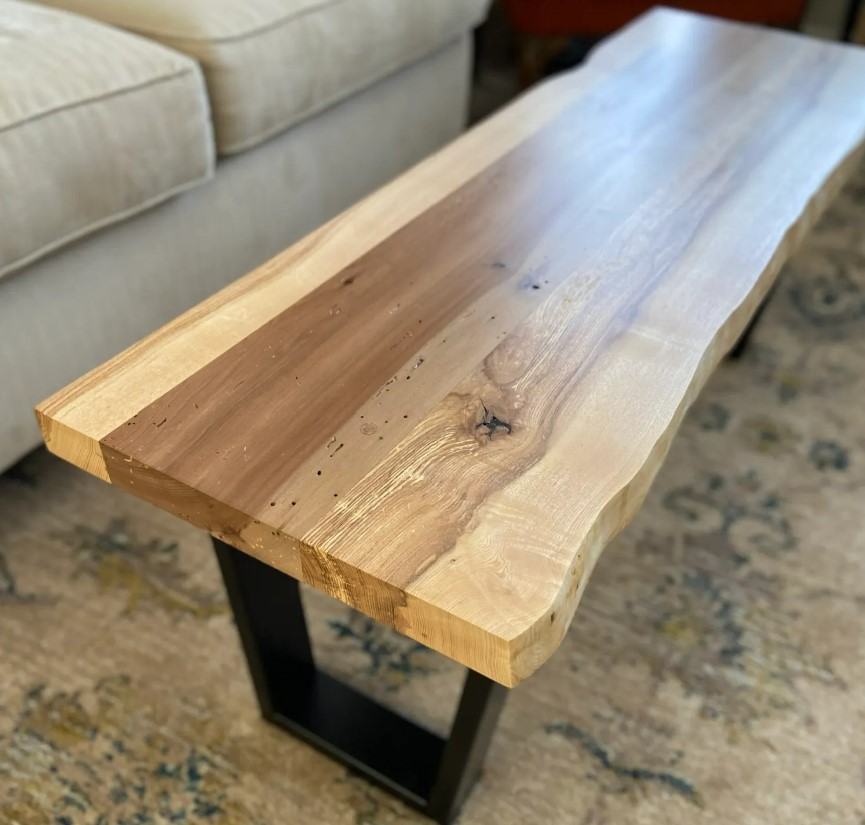
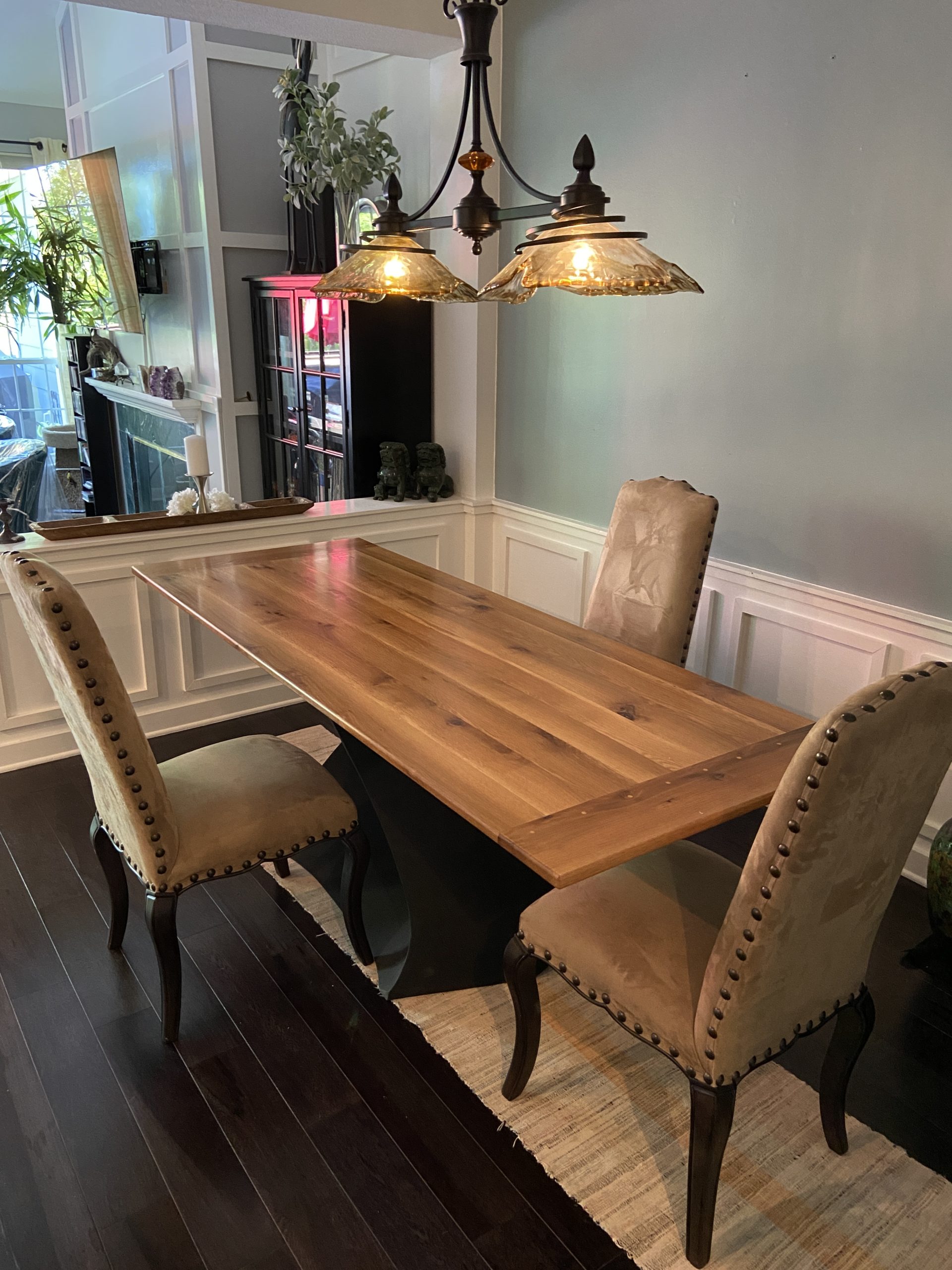
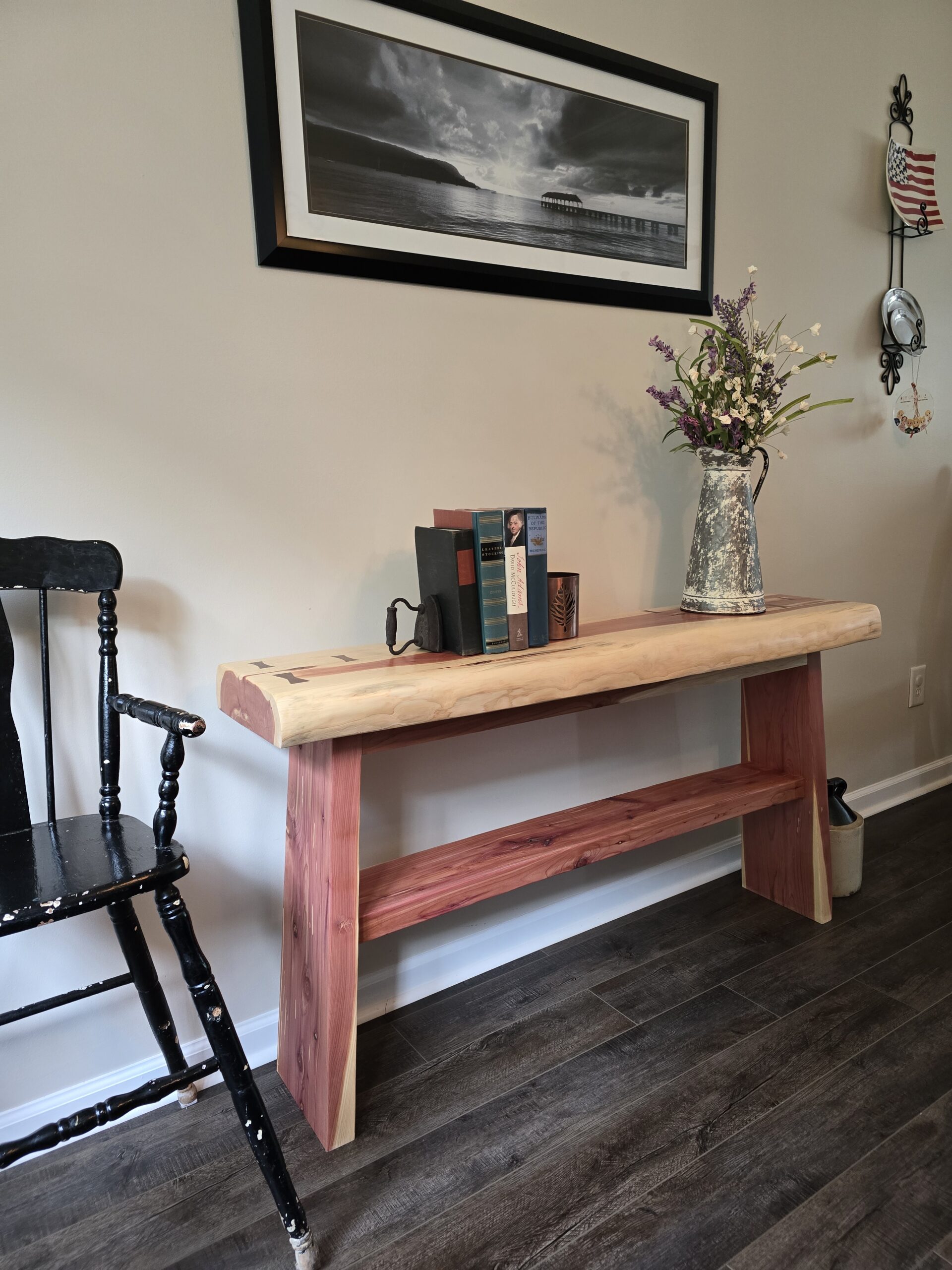